Robotic inspection and maintenance for the wind turbine industry
BladeBUG: BladeBUG robot, external protective casing prototype
To design and prototype an external protective casing for BladeBUG's existing robot so that it can be deployed in the intended extreme environment.
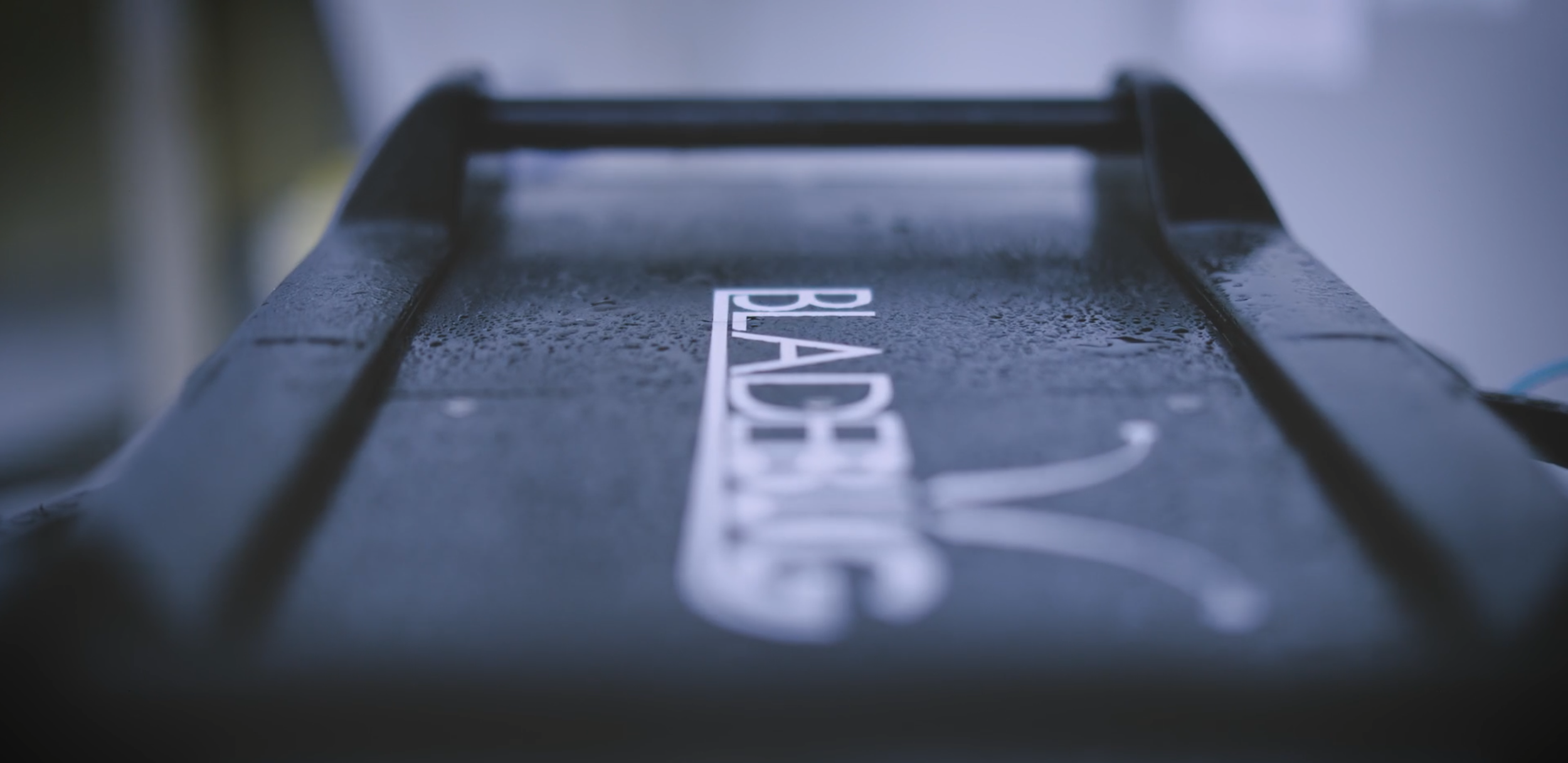
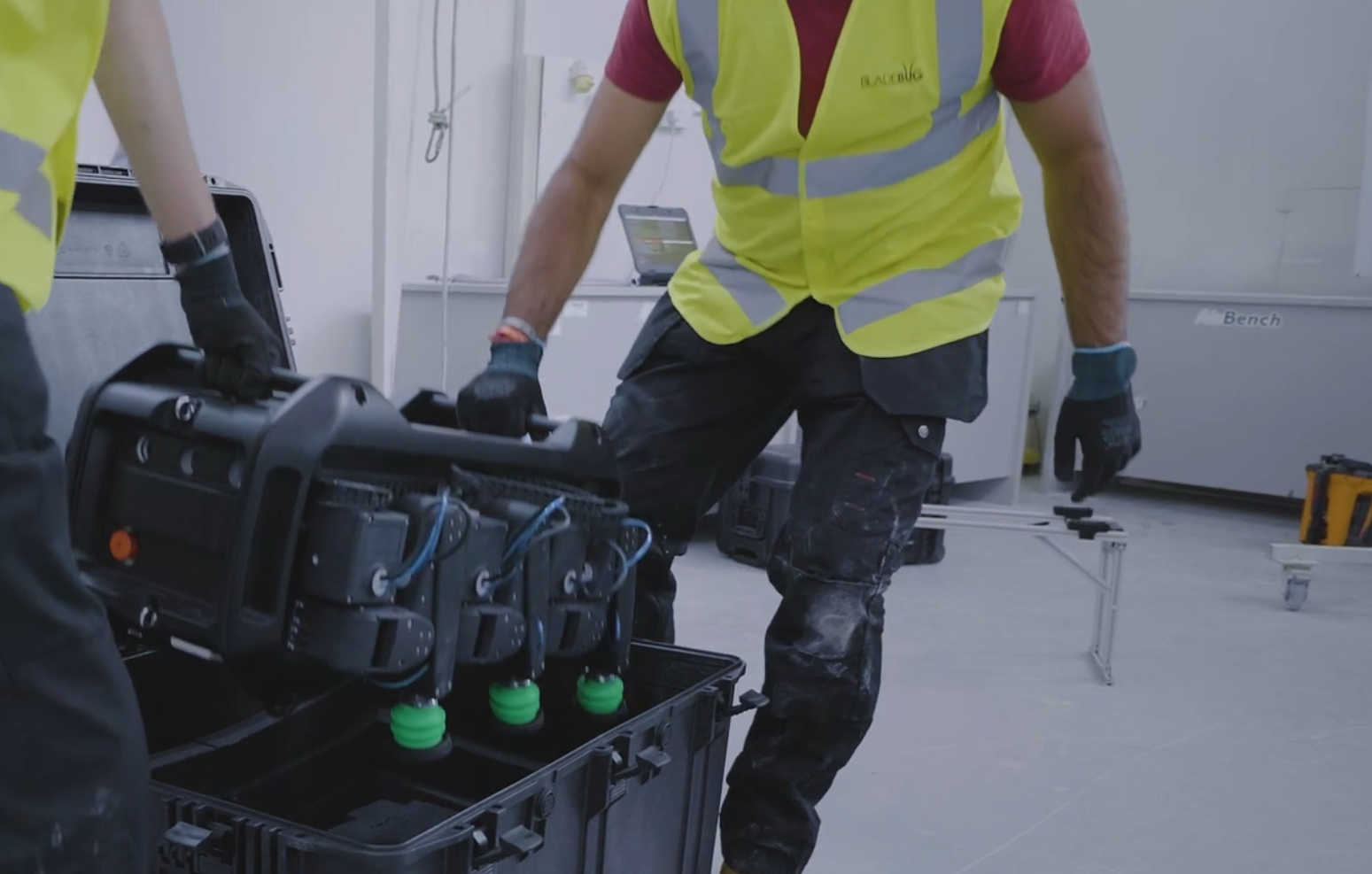
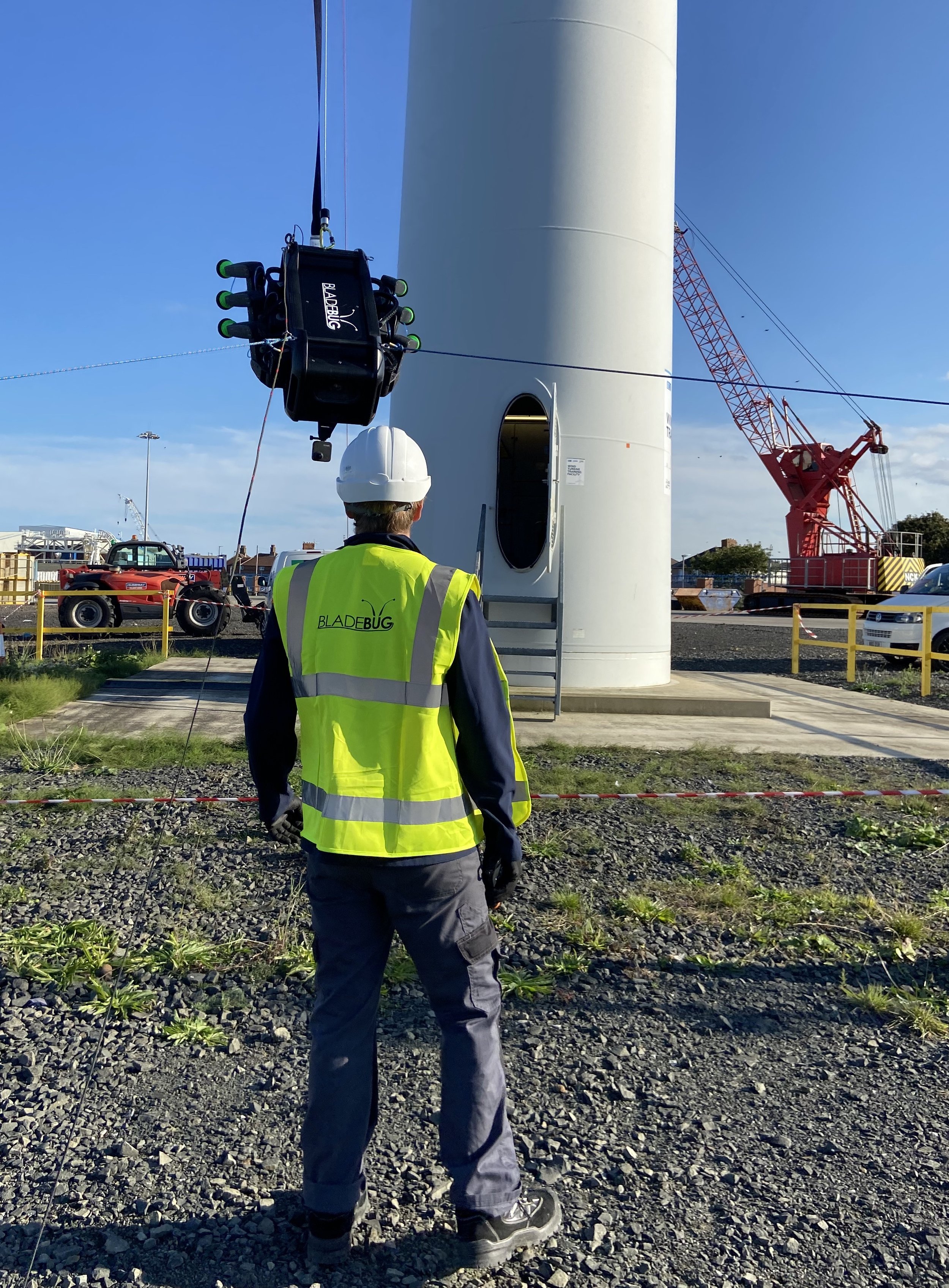
Description
BladeBUG need support to further develop their maintenance and repair robot for wind turbines as part of a €150k grant project from RIMA (Robotics for Inspection and Maintenance) network. The project focused on the robot’s industrial design, improving usability for professional users, and the robot’s suitability for use in extreme environments.
It resulted in an encased, conceptual robot for early adopters. The team worked on the industrial design of the external protective casing, as well as internal casings for the electronics. The project included in-depth user interviews to map and document the user requirements and context, to ensure improved usability and handling during deployment, transportation, and operation. It also evaluated and provided initial suggestions for the UI/UX of the control interface. The final stage of the project also included user testing and evaluation of the new casing.
Impact
The new aesthetics provides a sense of confidence that the robot is robust enough to manage the handling and environment of a wind turbine – on and offshore. Moreover, we have improved the experience of handling or manoeuvring the robot. Overall, the robot feels more rugged and able to withstand tough treatment during transport, deployment, and operation up on the nacelle and blade of a turbine.
Time frame of involvement: 18 months
Role: Team Lead
Responsibilities: Project manager, responsbile for team and budget tracking, Design Lead, Client relationship and contact, User research lead, RFP contributor
Team: EGGS Design: Johan Schreiner, Carl-Gustaf Lundholm, Katharina Brunner, Camilla Lundström
Budget: €120 000